Specifications
Featured Specs
Neck/Body Material | One-piece carbon fiber |
Overall Length | 23.2" (58.93 cm) |
Size | Concert |
Body Depth (Rear) | 3" (7.62 cm) |
Weight | 1lb 11oz (765 grams) |
Scale Length | 15.25" (38.74 cm) |
Number of Frets | 19 |
Tuners | KLŌS Featherlite Pro |
Strap Pin Buttons | Black Aluminum |
Strings | D'Addario Fluorocarbon |
Body Specs
Material | Carbon Fiber Composite |
Color | Black Carbon Fiber |
Finish | Gloss |
Body Length | 11" (27.94 cm) |
Width at Waist | 5.2" (13.21 cm) |
Width at Lower Bout | 8.3" (21.08 cm) |
Width at Upper Bout | 6" (15.24 cm) |
Bridge Style | String through body |
Bridge Material | Composite Ebony |
String Spacing at Bridge | 1.54" (3.91 cm) |
Soundboard Bracing | None |
Soundhole Diameter | 2.56" (6.5 cm) |
Neck Specs
Material | Black Carbon Fiber |
Finish | Gloss Lacquer |
Nut Width | 1.38" (3.51 cm) |
Fingerboard Material | Composite Ebony |
Fingerboard Radius | Flat |
Fingerboard Style | Traditional Acoustic |
Headstock Shape | Minimalistic |
Headstock Angle | 12 Degrees |
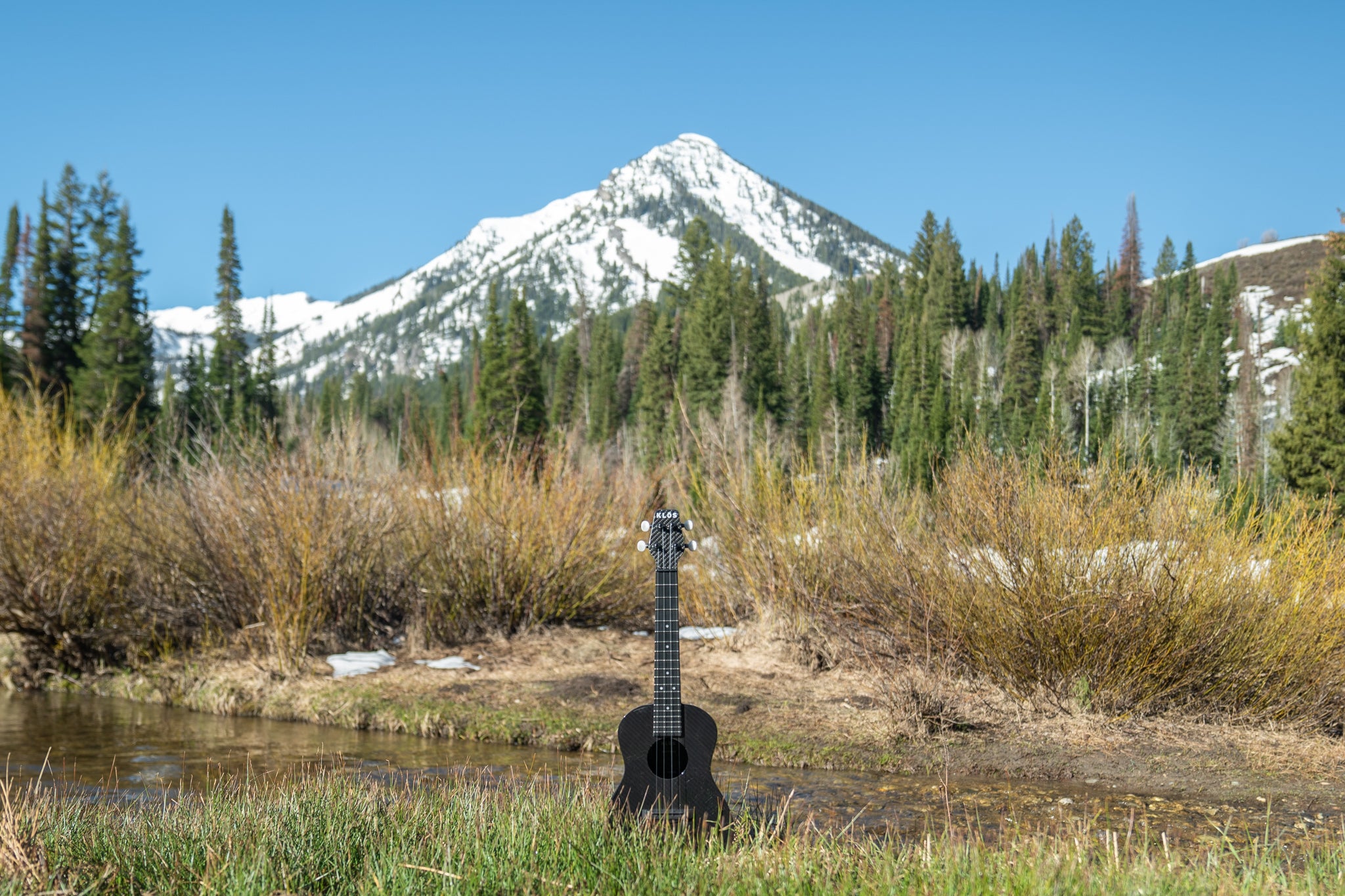
Venue: Anywhere
Concert On-The-Go
The KLOS Concert Ukulele offers a crisp, bright tone on a perfectly playable uke you can take anywhere.
Discover Carbon Fiber

Durable
Carbon fiber is extremely resistant to temperature and humidity, so our ukuleles stay in-tune longer and won't warp, bend or crack in different climates. You'll never have to tune in-between songs for the rest of your life.

Gliding
Carbon fiber's stability coupled with our state-of-the-art PLEK machine creates an unmatched play experience. Glide on a smooth fretboard that has impossibly low action and no fret buzzing

Defined
Carbon fiber's unique structure lets sound carry more cleanly through the material. On a concert ukulele, that means an articulate tone and unbelievable sustain.
A proprietary design that sandwiches closed cell foam between two carbon fiber soundboards. When coupled with our negative bracing, this technique improves your instruments strength and flexibility as well as enhances your music's volume, tone and sustain.

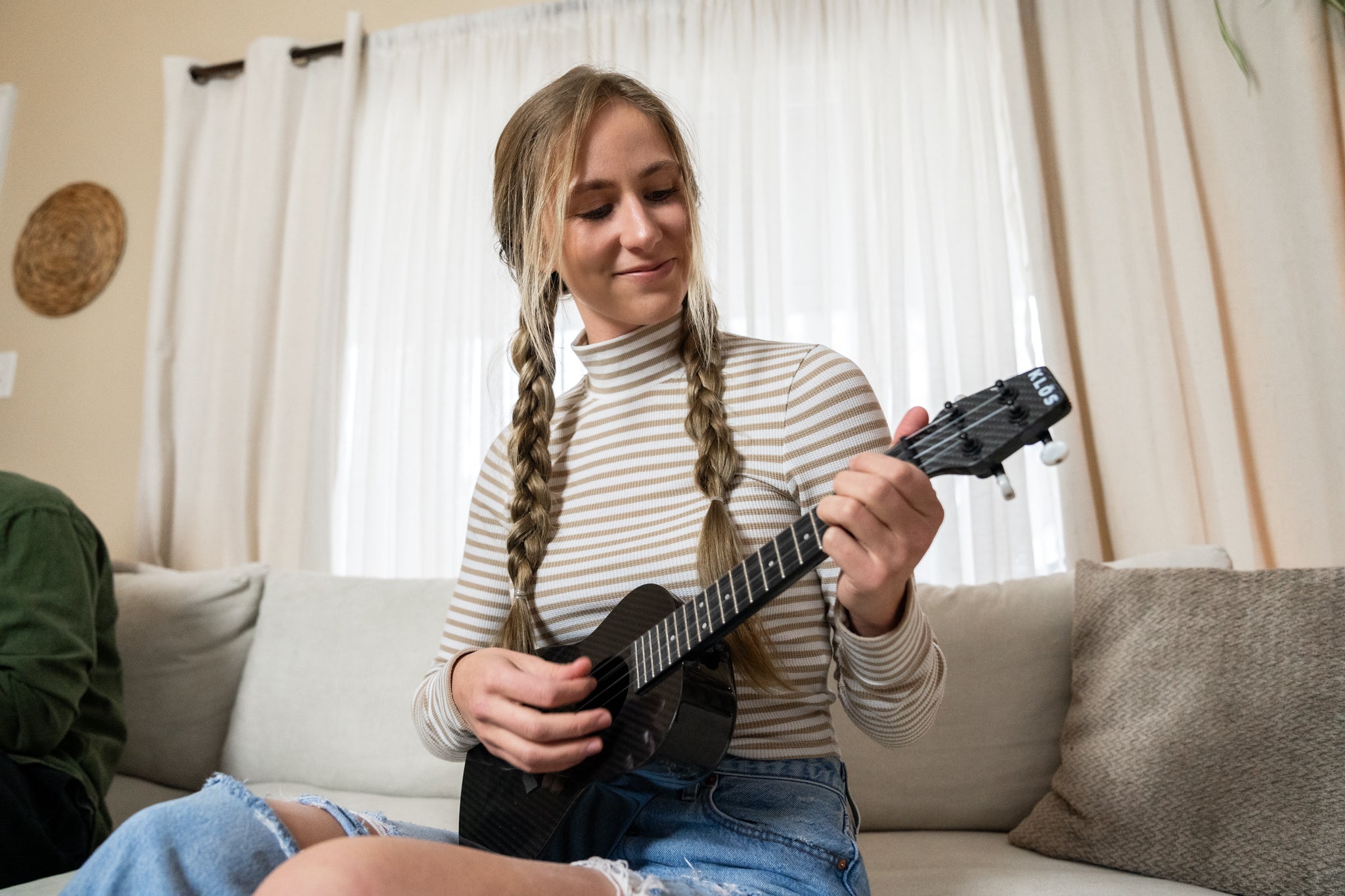
Can't put it down
Perfectly Playable
Low action and precision filed frets make a ukulele that's fun to pick-up-and-play.
Stunning sound
Incredible action and perfect playability compose a beautiful sound. Hear the KLŌS difference for yourself.
AUDIO SAMPLES
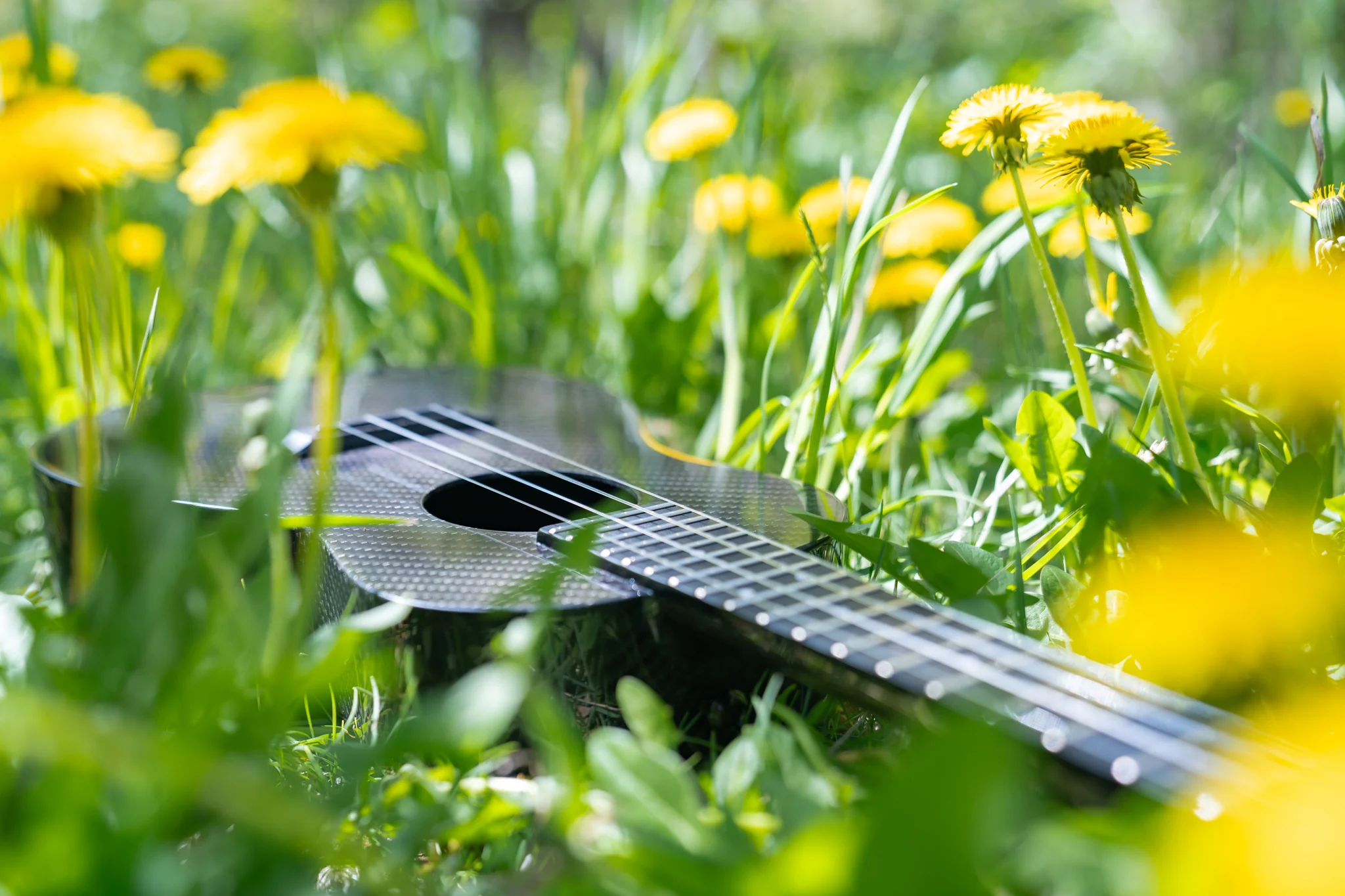
DRIVEN BY INNOVATION
Built from Tradition
We're taking classic instrument design philosophy and injecting vision of the future, making instruments you won't want to leave behind.
Materials
Your choice between two expertly crafted carbon fiber materials.
Our traditional black bi-lateral carbon fiber weave that you can see across all of our instruments since the beginning of KLOS. The sleek and defining "carbon fiber" style.


Like the look of wood but want the benefits of carbon fiber? Nickel-infused carbon fiber that's made to emulate the look of a wooden instrument with each instrument having their own one-of-a-kind pattern. Ideal for the traditionalist on the outside, but innovator on the inside.
Pickup
Plug in and unlock your instrument's potential.

An active piezo-electric system that captures the true acoustic essence of your ukulele. Measures string and instrument vibrations to deliver bright, clear tones with excellent string articulation. Powered by two 2032 coin batteries, it features an on-board integrated tuner for convenience. The result is a warm, full-range signal that represents the true character of your ukulele.